Accurate to the nearest hair is not precise enough
C 32 | C 42 | RS 2 | HS flex | SK Technology GmbH | Prototyping
SK TECHNOLOGY is formidable when it comes to precision. That’s the result of an awareness that minute subtleties are the difference between acceptance and rejection – and a stock of machinery that can withstand critical inspection down to the micrometre range. This is where Hermle succeeds. Six automated 5-axis machining centres allow the cutting expert to be really picky.
Benedikt Kulzer often speaks in terms of superlatives. And rightly so: after all, SK TECHNOLOGY GmbH manufactures components and assemblies with a dimensional accuracy of 0.3 micrometres – a fraction of the width of a human hair. "The challenge is to achieve maximum precision with a very high degree of complexity within a very short time and with extreme reliability", explains the managing director, who is now the second generation to head up the family-owned company.
Delivering very high standards of precision was always the motto of company founders Johann Stangl and Stefan Kulzer. In 1988, the two work colleagues set up Stangl & Co. GmbH Präzisionstechnik in the German town of Roding with the intention of manufacturing products to their standards. They transported the first machine, a lathe, on a trailer to the town in the district of Cham in eastern Bavaria. Two years later, they moved out of the barn into a new production facility with 1,300 square metres of floor space, which they subsequently extended in 1994 and 1997 to 4000 square metres. In 2008, they opened a second plant in the town of Waldmünchen. At its head office, SK TECHNOLOGY invested in more space in 2015 and installed an air-conditioning system to meet stricter requirements in terms of precision and cleanliness. Benedikt Kulzer has managed the company together with his father since the end of November 2019, and they renamed it SK TECHNOLOGY GmbH in 2022. Today, the system supplier employs around 300 people at two locations.
Across a total floor space of 15,000 square meters, they manufacture prototypes, individual parts and small to medium production runs for industries such as aerospace, medical technology and mobility – from motorsports to commercial vehicles – and for the energy and semiconductor sectors. "We deliver a degree of precision that only a few companies in German can offer", emphasises Kulzer. And before you accuse him of going too far with his assertion, it’s worth listening to what he has to say. He talks about a cutting machine that constantly alternated between producing good parts and reject parts after it was moved to a different location. Its precision fluctuated by 0.01 millimetres – despite being in an air-conditioned environment. "Ultimately, we discovered that the minimal draught created when the staff entrance was opened was enough to put it outside the tolerance range".
A strong basis for the highest goals
What’s the secret behind this precision? He cites the interaction between humans, the machine and the air-conditioned environment. "The torque to ensure proper clamping is just as important as the water quality and water temperature of the cooling lubricant", explains Kulzer. However, there are degrees of fineness that have a decisive influence over the very highest levels of precision. "The successful pursuit of absolute perfection also depends on the fundamental precision of the machine", says Kulzer. "The milling centres by Maschinenfabrik Berthold Hermle AG are the ideal basis for us. That’s because the more precise they are, the higher the achievable level", adds the managing director.
The cooperation with Hermle dates back to before his time: "The second or third machine was already from Gosheim", says Kulzer. This often made them a role model for other companies, although this certainly wasn’t the only argument in favour of purchasing for him. "It had to do with everything that came with the machines: the right service package and trouble-free cooperation were just as important to us as the reliability and precision of the machines", explains Kulzer.
-
Benedikt Kulzer, Managing Director of SK TECHNOLOGY GmbH -
One of the Hermle RS 2 robot systems only handles pallets. -
Two systems are quick to learn: According to SK TECHNOLOGY, the changeover from the SOFLEX robot control system and the Hermle "Automation-Control-System" (HACS) worked seamlessly. -
Growth within one year: after commissioning two new C 32 U machines with robot automation in mid-2021, SK TECHNOLOGY had already invested in a C 42 U with HS flex in January 2022.
Is a robot worth it?
In 2016, the family-owned company introduced its first milling process with a new Hermle system: two C 32 U machines with an RS 2 robot system. The managers were initially unsure whether and how to automate the 5-axis machining centres. "We drove to Gosheim to visit Hermle with six components and several questions. I was most interested to discover whether it would also make financial sense with smaller quantities", recalls Matthias Bücherl, Head of the Milling Department. After a test run and a discussion with Hermle, one thing was clear to him: "It was definitely viable".
The robot can handle pallets as well as individual workpieces. This gives SK TECHNOLOGY maximum flexibility – even though pallet handling is gradually becoming the predominant method. "Some of our components cannot be machined in just one clamping set-up due to their size, geometry or complexity", explains Kulzer. This was why, convinced of the benefits of automation and driven by a lack of capacity, the robot system for the second machining cell that he ordered in mid-2021 was specified to offer pallet handling only. Here too, automation was used for two C 32 U machines. Both production cells were soon operating at full capacity. When incoming orders accelerated once more at the end of 2021, the entrepreneur was already planning the next investment.
Quicker ramp-up thanks to standardisation
In 2022, SK TECHNOLOGY purchased two C 42 U machines with the HS flex system. The switch from the robot to the flexible handling system was surprising to begin with. "Ideally, we would have accommodated both machines in our second plant in Waldmünchen, where we had not yet introduced any automation to date. However, despite playing a lot of ‘Tetris’ games, we finally realised that we simply didn’t have enough space", says Kulzer. For the workers there, the C 42 U with HS flex presented two challenges simultaneously: not only did they have to learn the automation process but also the new user interface for the 5-axis milling centre. "Hermle’s proprietary HACS operating software is so intuitive that the familiarization process was completed within a very short time. In Roding, it felt like only a matter of hours before the team was ready to hit the ground running", recalls Kulzer. He adds that this was also thanks to Hermle’s consistent operating concept: "The employees here know the interface, the machines, the little details that go into them. Added to this is the reliable and competent service". As a result, the changeover from the SOFLEX robot control system to the Hermle Automation Control System (HACS) was seamless.
Initial scepticism concerning profitability was soon replaced by conviction. As a matter of principle, Kulzer no longer buys anything without automation because it allows him to expand his production capacity without worrying about staff shortages. In Roding, for example, a maximum of two employees per shift are needed to operate the five automated Hermle machines. With three shifts per day where the third shift only requires one employee, it still works out: SK TECHNOLOGY has five machines in Roding operating non-stop 24 hours per day – and only needs a total of five employees. The key factors here, as he explains, are to understand the automation and to plan the work steps as far in advance as possible so that the systems can run for two or three days – using components made of plastic, aluminium, steel and stainless steel. In this context, the machining time is between ten and 60 minutes for individually handled parts and up to eight hours for workpieces clamped onto the pallets.
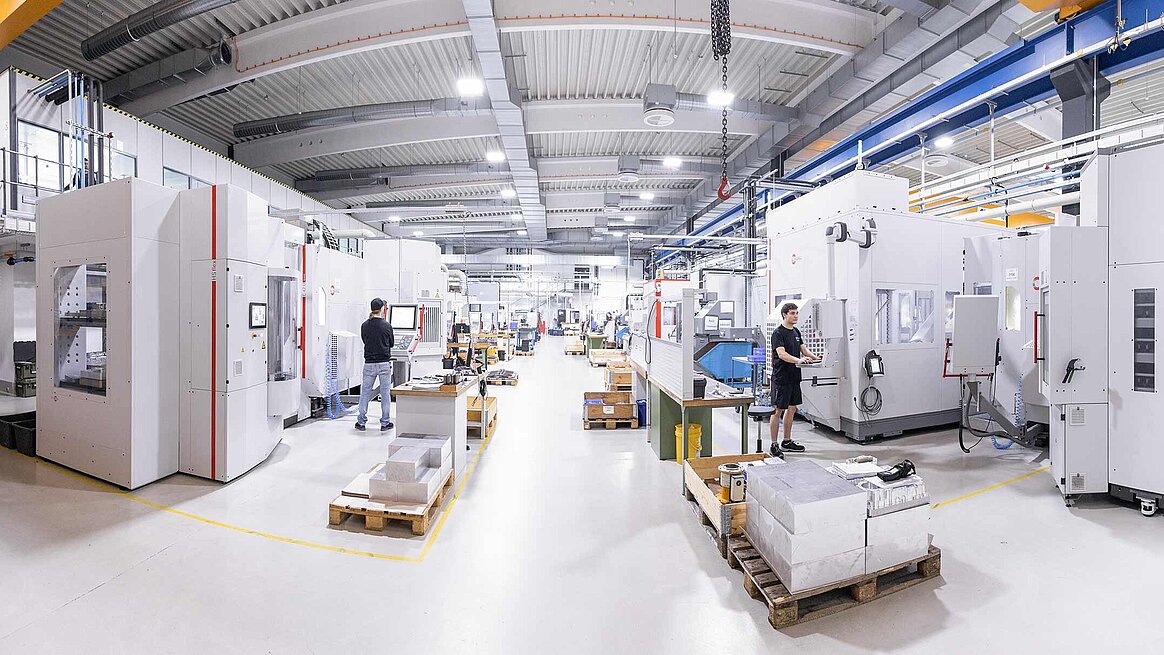
Precision, universally usable
The automation of the Hermle machines not only gives SK TECHNOLOGY added flexibility to take on more orders. It has also enabled the manufacturer to become part of the supply chain of its customers – and it now handles volumes of between 5,000 to 10,000 units with ease. "Thanks to the robot and the HS flex system, we now produce pre-production parts until the relevant component enters large-scale production", explains Kulzer. This also benefits capacity utilisation: "A planning horizon of six weeks is normal for a contract manufacturer. We now operate to a horizon of six months and more", says the managing director. Contract manufacturing is also characterised by the wide variety of parts to be machined. "Since we will definitely be using the Hermle machines to produce parts for the next six to ten years, they must not only be precise and powerful but also universally usable. This means that we are equipped to meet all possible new challenges", says Kulzer with confidence.