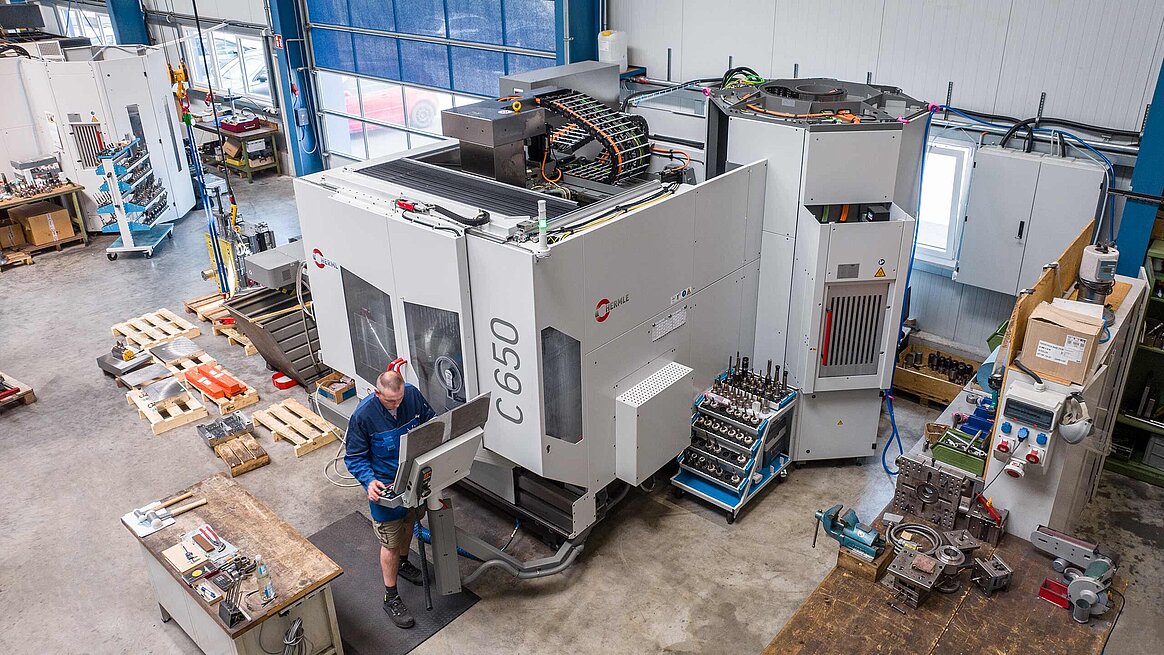
COPPER INSTEAD OF COOLING DUCT
A tour through the operating facilities with about 50 employees is as impressive as these details would suggest: The facility is made up of multiple interconnected halls arranged in rows, so the visitor becomes disoriented after making the third turn. The tour ends back in the Managing Director's office with the inconspicuous mould core that is responsible for the hollow area in the pincer grip on the table.
The more delicate and intricate the geometry, the more difficult heat management becomes. The alternative to copper is thin cooling ducts. For temperature control ducts that follow contours, they can be laser-sintered or vacuum-welded. "The danger here is that these very narrow cooling ducts become clogged over time. Regular tool cleaning is necessary to prevent this", comments Starch. MPA technology offers a smart solution in this case: Copper dissipates heat out of the narrow areas. The copper segment ends where the cooling ducts have enough space. The cooling water can flow here without difficulty.
SUPERSONIC MATERIAL APPLICATION
How does the copper get in the core? For this purpose, HMG has developed the MPA 42, based on the C 42 U five-axis milling centre, which can not only remove but also apply material. Heat, nitrogen, superheated steam and a de Laval nozzle are the critical factors for accelerating the metal powder to supersonic speed so that it coalesces with the clamped blank upon impact. The five axes of the machining centre align the stream of powder at almost any angle to the component, thereby allowing the cooling duct or copper inlays to form even on curved surfaces. Finally S&S obtains a soft core. "Then we manufacture the outer contour here", reports Starch. Correct data is important for this. "Our designers know exactly the position of the copper filling. In this way we are able to produce delicate and intricate cores with optimum heat dissipation.“
The Managing Director's preferred additive manufacturing process is MPA technology. Why? Other than the copper portion, of course, the core consists of the same material as the rest of the mould – tool steel. "Thus we have a component with the same properties and the same service life as the mould cavity. This doesn't work with other additive processes", emphasises the mechanical engineer. It is not news that copper is better at conducting heat: "Previously we simply drilled a hole and pressed a copper wire into it. That was not a particularly flexible approach with regard to the contour and shape of the cooling area", concedes Starch. There is also a danger that small air pockets will prevent the flow of heat. He first learnt of the HMG additive manufacturing process through Gardena, which already had a tool with vacuum-soldered injection moulding tools in operation and saw potential for optimisation.
THE BEST OF BOTH WORLDS
Starch is convinced by MPA technology. This technology makes it possible to manufacture complex moulds while at the same time ensuring efficient heat dissipation. He would recommend this for his customers if they want to increase economic efficiency through optimised cooling capacity in especially small areas and see justification for the additional costs involved. "It is a qualitative, highly functional solution, but not an inexpensive one", acknowledges the mould maker . His designers and technicians also have a positive assessment of the technology: "There are no problems in the application. With the combination of MPA technology and conventional temperature control technology, we achieve the best results and meet our customers' needs."