Flexibility thanks to robot automation
C 32 | RS 1 | SWACRIT systems GmbH | Medical technology
SWACRIT systems GmbH specialises in the production of top-quality composite parts, mechatronic assemblies and high-precision mechanical components. To enhance productivity and efficiency, the high-tech company based in Tyrol, Austria, has invested in HERMLE's RS 1 robot automation solution, which enables the flexible and continuous manufacture of individual parts and components on pallets.
SWACRIT systems is a strategic partner for complex solutions and specialises in designing and producing high-precision systems for medical technology, scientific instruments and vacuum technology. Established in 1963, the company presently boasts a workforce of approximately 190 people, including 13 apprentices, and operates from two locations in the Austrian region of Tyrol. The core expertise at the location in Wildermieming is joining technology. This is where, the company, in its role as a system supplier, caters to the semiconductor, coating and R&D markets, as well as to the requirements of manufacturers of analysers and treatment devices. The core expertise in Hall in Tirol lies in precision machining, specifically tailored to the medical technology and instrumentation sectors. At both locations, achieving the highest quality is the top priority, as evidenced through certifications to EN ISO 9001, as a manufacturer of medical products to EN ISO 13485 and as an established partner of the aerospace industry to EN ISO 9100. “The perfect blend of mechanical production, precision engineering, innovative joining techniques, vacuum brazing and clean room assembly makes us a highly sought-after system supplier. We have always prioritised long-term partnerships and think of ourselves as a production and innovation partner for our customers – often in a ‘single-source’ capacity,” says Anton Aigner, production manager at the Hall in Tirol location.
-
The robot system at SWACRIT systems consists of two HERMLE C 32 U 5-axis machining centres and the RS 1 robot system. -
SWACRIT systems is a system supplier for the medical technology, instrumentation and vacuum technology sectors. -
SWACRIT systems boasts state-of-the-art measuring equipment with 3D measuring systems and surface testing devices. -
The robot supplies both HERMLE machining centres with components around the clock. Three rack storage modules, featuring die and pallet pockets as well as clamping device and gripper pockets, ensure the optimum provision of parts. -
Successful cooperation: Milling shift supervisor Matthias Prem, production manager Anton Aigner (both SWACRIT systems) and Gregor Rofner, sales engineer at HERMLE Austria. -
Der Roboter bedient beide HERMLE-Bearbeitungszentren mit Bauteilen rund um die Uhr. Drei Regalspeichermodule mit Matrizen- und Palettenplätzen sowie Spannmittel- und Greiferplätzen sorgen für eine optimale Teilebereitstellung. -
Gregor Rofner schätzt die Zusammenarbeit mit SWACRIT systems und freut sich, mit dem Unternehmen in Zukunft auch weiter zu wachsen.
System supplier for highly complex components
The Hall in Tirol location primarily focuses on precision machining of predominantly highly complex components. In addition to titanium and CoCr alloys (both cast and forged), the facility also processes a range of materials, including various stainless steels, aluminium, copper and nickel-based alloys. The modern machinery comprises ten turret lathes, nine machining centres (six of which are automated) and five grinding machines. Furthermore, SWACRIT systems boasts state-of-the-art measuring equipment, a dedicated finishing department as well as a 600 m² clean room area and a 300 m² controlled area designated for assembling individual parts into complete assemblies and for component assembly.
The Austrian company has been focussing on automated machining technology for more than ten years. “We put the first automated system into operation back in 2013, at that time without any intelligent control. In 2018, we took a significant step by investing in HERMLE automation with HS flex, thereby incorporating an intelligent control for the first time. By implementing this system, we have achieved a substantial improvement in terms of productivity and cost-effectiveness, and we have steadfastly continued along this trajectory,” explains the production manager.
Flexibility thanks to automation
The business is now thriving, with turnover more than doubling over the past four years alone. Given the extensive range of components available at SWACRIT systems, maintaining maximum flexibility in production is of paramount importance. “Between five and seven different components run in parallel on our automated machining centres, often involving up to ten different clamping setups per machine. On average, we still achieve over 5,000 spindle hours per machine each year – an impressive benchmark,” adds Aigner. SWACRIT systems operates in two manned shifts during the day and employs unmanned operations during the night and over the weekend. According to Anton Aigner, effectively managing the substantial volume of parts within an automated system necessitates well-defined and elaborated processes. This applies particularly to order creation, planning, work preparation, CAM programming and downstream processes such as finishing and quality assurance: “Over the past decade, we have accumulated substantial experience in this domain, consistently refining and enhancing our processes.”
Parts and pallet handling in demand
While in the past, the machinery was designed to be as flexible and as universal as possible, the company now focuses on selecting new machines based on product groups and specific applications. Since the decision-makers in Hall in Tirol were not entirely satisfied with the autonomy times of the existing systems, they sought an appropriate solution. “Due to our extensive variety of parts, with an average batch size of 20 to 40 components, and the need to produce individual parts and components on pallets within a single system, automation with a robot was the only viable option for us,” explains the production manager, outlining the decision behind choosing a robot solution.
Gregor Rofner, the responsible sales engineer at HERMLE, wholeheartedly agrees: “SWACRIT systems is, if you like, the perfect HERMLE customer: High precision, small batch sizes, flexible operations and a diverse range of materials – these are all aspects where we can bring our strengths fully into play. A two-machine solution with the RS 1 robot system is ideal for achieving the desired high level of flexibility and cost-effectiveness.”
One robot supplies two HERMLE C 32 U machining centres
The system at SWACRIT systems consists of two HERMLE C 32 U 5-axis machining centres and the RS 1 robot system, which supplies both machines around the clock with the help of a Kuka robot. Three rack storage modules, featuring die and pallet pockets as well as clamping device and gripper pockets, ensure the optimum provision of parts. The RS 1 robot system thus serves as a combination cell for pallet and workpiece automation and can be docked to various HERMLE machining centres “It makes no difference whether one, two identical or two different machine models are interlinked. With the one-machine solution, the cell is controlled using the HERMLE Automation Control System (HACS), while the two-machine solution utilises the Soflex production control system, as implemented here at SWACRIT systems,” explains Rofner, highlighting the high-level flexibility of HERMLE automation. The robot has a maximum handling weight of 60 kg. “Three key factors were crucial in our decision to choose HERMLE. Firstly, the highly effective technical solution. We were particularly impressed by the combination of a long-stroke clamping device and an NC-controlled interchangeable gripper, as it allows for the effortless handling of components ranging from 20 to 110 mm with a relatively small number of clamping devices. Secondly, HERMLE provides both the machine tool and the automation solution from under one roof, and thirdly, the exceptional service we receive,” notes Anton Aigner, when citing the reasons for choosing to work with HERMLE.
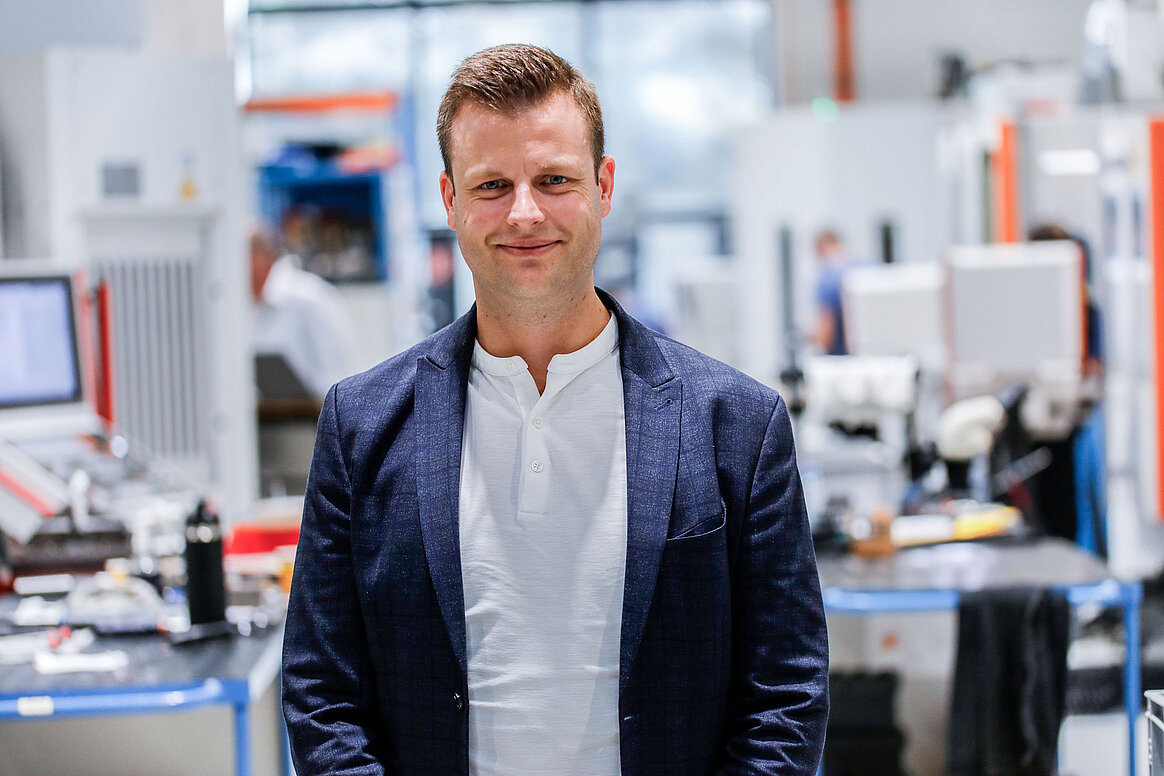
The right decision
“The cooperation with SWACRIT systems is excellent. We delivered the first HERMLE machine in 2018 and have since installed six further machines, with two additional machining centres in the pipeline. This naturally makes us proud, and we look forward to continuing to grow with SWACRIT systems in the future,” says Gregor Rofner, who is delighted with the excellent collaboration. Anton Aigner can only agree with this statement: “Through the acquisition of the RS 1 robot system, along with the two C 32 U 5-axis machining centres, we have taken a significant leap forward in terms of flexibility, precision, productivity and process reliability. The decision to tackle the challenge of automation together with HERMLE was a resounding success, and we would make the same choice again without any hesitation.”