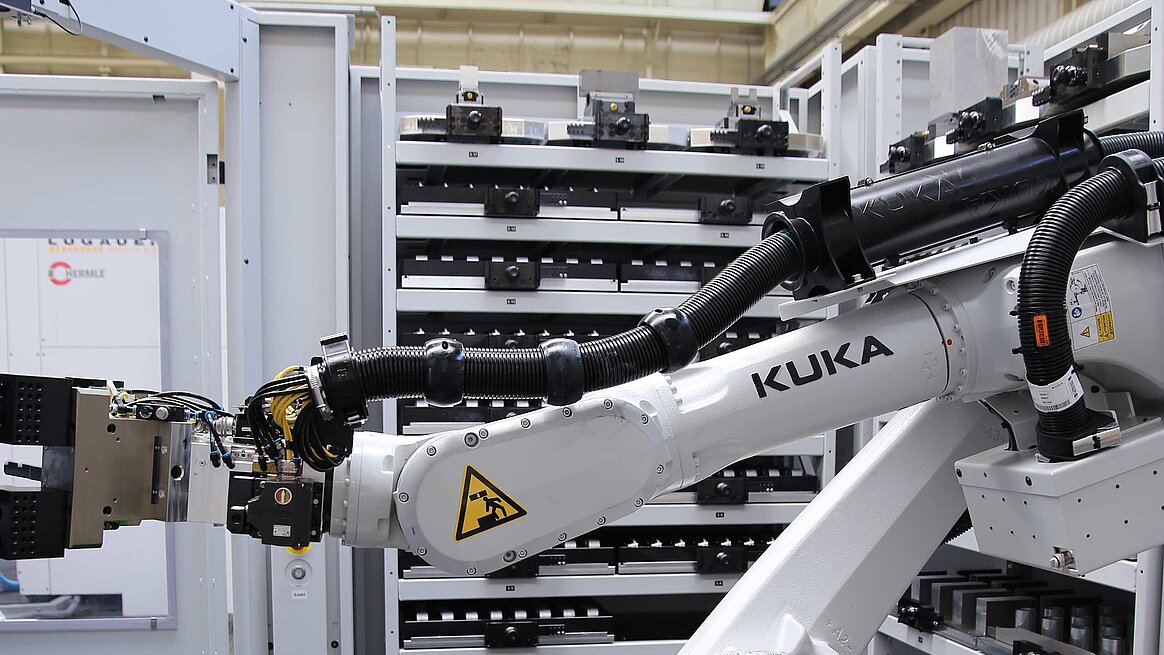
Spindle runtimes optimised: 24/7
According to Christian Aigner, authorised signatory and technical manager at Lugauer, the extensive flexibility of the overall system is just amazing: "In the first shift, we produce individual parts on the first machine followed by unmanned pallet or handling parts production. A component for the automotive industry is currently manufactured 24/7 on the second machine. On this machine, we now produce the same number of parts in one week with two people as we did before with two machines and four people. It's beyond our wildest hopes," Aigner says proudly.
Generally speaking, the rack storage concept ensures an exceptionally high autonomous runtime, as the gripper and device changeover takes place automatically. The full-scale setup station also enables pallets and workpiece carriers to be set up during the primary processing time. "At first, it was an enormous change for our staff. The software, working with the robot and the process of handling blanks were all new, and they had to learn to think ahead. Both machining centres operate unmanned at night or over the weekend, meaning a certain amount of setup preparation is necessary," the technical manager says when pointing out possible teething problems. The training provided by Hermle to the Lugauer team during the initial training period and subsequent work processes focused on these and other soft skills. "In the meantime, everything works just fine," Aigner says.