Going the extra mile
Maximum precision in tool and spindle technology – Goldring tool holding fixtures are a prime example of this. Helmut Diebold GmbH & Co. manufactures high-end accessories for CNC machining. The company uses automated processes, for example the combination of a HERMLE C 42 U five-axis machining centre and the RS 2 robot system.
Significantly more precise than the standard approach – perfectly sums up the motto of Hermann Diebold. "Is it worthwhile?" the managing director wonders. And answers his own question: "No. We don’t earn more money as a result, but customers value the quality of our components and choose us for that reason. And if I didn’t have that level of precision, I’d want it."
In 1952, Helmut and Ida Diebold founded Helmut Diebold GmbH & Co. in the southern German town of Jungingen. Their aim was to manufacture precise system components for the construction of textile machines. Over the years, the company has gone from being a subcontractor to a globally renowned manufacturer of precision tools. Today, the range includes high-quality Goldring tool holding fixtures, innovative shrink units, precise measuring technology and advanced spindles.
Boasting more than 70 years of experience and 120 specialised employees, the company attaches great importance to the highest levels of precision and process reliability. "Our products need to fit perfectly into the overall machine-spindle-tool system," explains managing director Hermann Diebold, who is the second generation to manage the business. "It’s the only way to work safely at speeds in the high five-digit range." Diebold additionally helps its customers maximise productivity and efficiency through comprehensive service offerings, including calibration and repairs.
Fresh input
Over the decades, the company has repeatedly set new technological milestones, particularly in the field of shrink technology. As a pioneer, Diebold quickly became a market leader with its process that ensures exceptionally rigid and secure tool clamping. What once required laborious heating with a welding torch is now fully automated. The latest generation of shrink units measures temperatures independently, prevents overheating and cools down automatically – all at the touch of a button. "Our ‘OneTouch’ facilitates operator tasks and makes processes safer," explains Hermann Diebold.
Automation for him is not an end in itself but an essential means of increasing productivity. "We realised early on that machines need to be not only more efficient but also smarter," he recalls. There is way too much downtime when working with machines without automation. Thanks to modern machining centres, such as the C 42 U with connected RS 2 from HERMLE, the company produces high-precision components in unmanned shifts. "We purchased our first C 42 U, knowing the level of automation would expand significantly with an additional machining centre. And that’s the reason why we’ll be adding a second machine soon," reveals Hermann Diebold.
-
Diebold has been using a C 42 U in combination with the RS 2 robot system since 2016. -
Seamless communication between the machining centre and the robot system optimises workflows and minimises downtime. -
-
The only limiting factor is the number of pallet spaces – thanks to the RS 2, Diebold produces unmanned at night and at weekends. -
Marcel Heck, CNC miller at Diebold, clamping the next component. -
The average runtime is 20 to 40 minutes; the RS 2 robot system exchanges the pallets without any manual intervention. -
Diebold manufactures spindles of the highest quality on the C 42 U, for example. -
Hermann Diebold: "Our customers know exactly why they choose Diebold: They receive products that go far beyond the norm – as we won’t accept anything less." -
Marcel Heck, CNC miller, and Hermann Diebold, managing director (from left), both Helmut Diebold GmbH & Co.
And it keeps on running ...
The C 42 U mills complex workpieces at full power – precisely and highly dynamically. The RS 2 robot system boosts flexibility by autonomously exchanging components during continuous operation. The machine and robot speak the same language, ensuring a seamless workflow and preventing downtime – even at night or at weekends. The ZM 192 additional magazine stores enough tools for extended jobs. The result: Significantly reduced throughput times, less costs and maximum process reliability – all without compromising quality or precision. CNC miller Marcel Heck says: "While the machine is running, I can focus on other tasks." He also praises the Heidenhain software: "Thanks to the dynamic preview and smart functions, I’m always in full control."
A key advantage of automation is the consistently high quality – from batch size 1 to 100. "Many of our workpieces are so precise that we measure each one immediately as the machine produces the next." The company also machines less critical components at night and at weekends. "The only limiting factor is the number of pallet spaces," says Hermann Diebold. This is because most parts run on the machine for 20 to no more than 40 minutes. In this regard, he is especially proud of his employees: "It’s not uncommon for our employees to stop by the factory briefly on a Saturday to replenish the machine. Many of them apprenticed with us, are highly motivated and want to achieve something."
Data is the gold of the future
Diebold focuses not only on mechanical precision for its own products but also on digital solutions. Especially exciting: A new partnership with a start-up from the University of Hanover, which develops sensor technology for machine data acquisition. "These magnetic sensors enable real-time monitoring of machine statuses, even in older systems without modern controls," explains Hermann Diebold. Artificial intelligence analyses the acquired data, thereby enabling predictive maintenance. The aim: To improve efficiency. "I thought it was a joke when I first heard that visualising machine statuses could boost productivity by 15 per cent. Today, I know: It’s no joke." It also enables tracking and planning of individual orders, as well as comparing planned and actual times. "That’s something we definitely need nowadays. The cost pressure is immense, and we need to maximise every bit of potential to its fullest."
And of course, the entrepreneur also relies on digital support for the HERMLE machine. As a central monitoring tool, the HIMS (HERMLE Information Monitoring Software) provides a compact overview of the C 42 U with live status. All the data, including data from the past, can be analysed in detail and exported. In the event of an error or issue, the system informs the user by e-mail via the HIMS server. "This means we know for sure if and when we need to intervene," explains Hermann Diebold.
Climate-neutral production
In addition to accuracy and innovation, the entrepreneur also champions sustainability. Diebold’s production is virtually climate neutral: "We rely on a mix of energy that does without fossil fuels," claims the managing director. The production halls are well insulated and the tool specialist obtains its heat from a neighbour who generates bioenergy from wood and wood chips. The waste heat from the compressors supplies the underfloor heating system. Diebold also uses several systems to air-condition its production facility: Up to an outside temperature of around 12°C, fresh air cools the circulation water; above this temperature, the company uses water from a local stream as the cooling medium. An extra ventilation and air conditioning unit with high heat recovery is only required for cooling during the hot summer months.
The stable room temperature ensures workpieces, tools and machines operate under optimal conditions and guarantee maximum accuracy. "The more demanding our customers are, the more we like it. Because it’s our quality that sets us apart from the rest." And something else is crucial: "Top products offer the longest lifespan – and that’s true sustainability. This is another reason why we rely on machines from HERMLE."
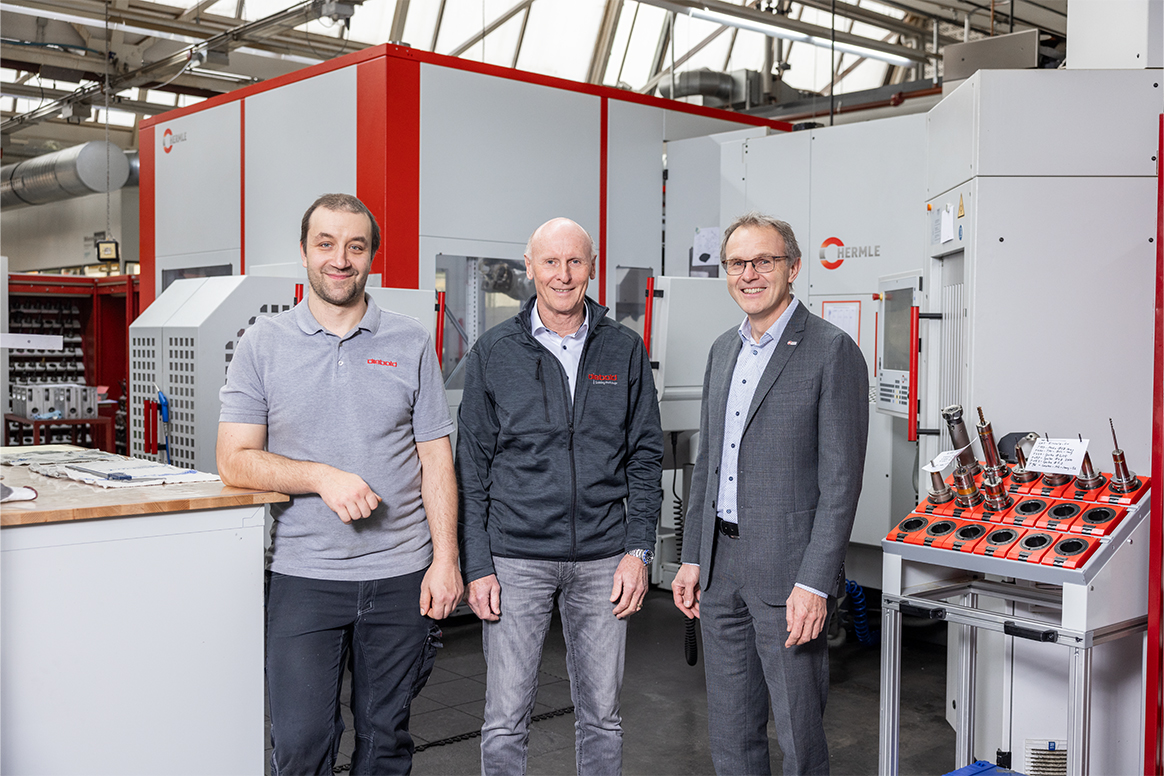