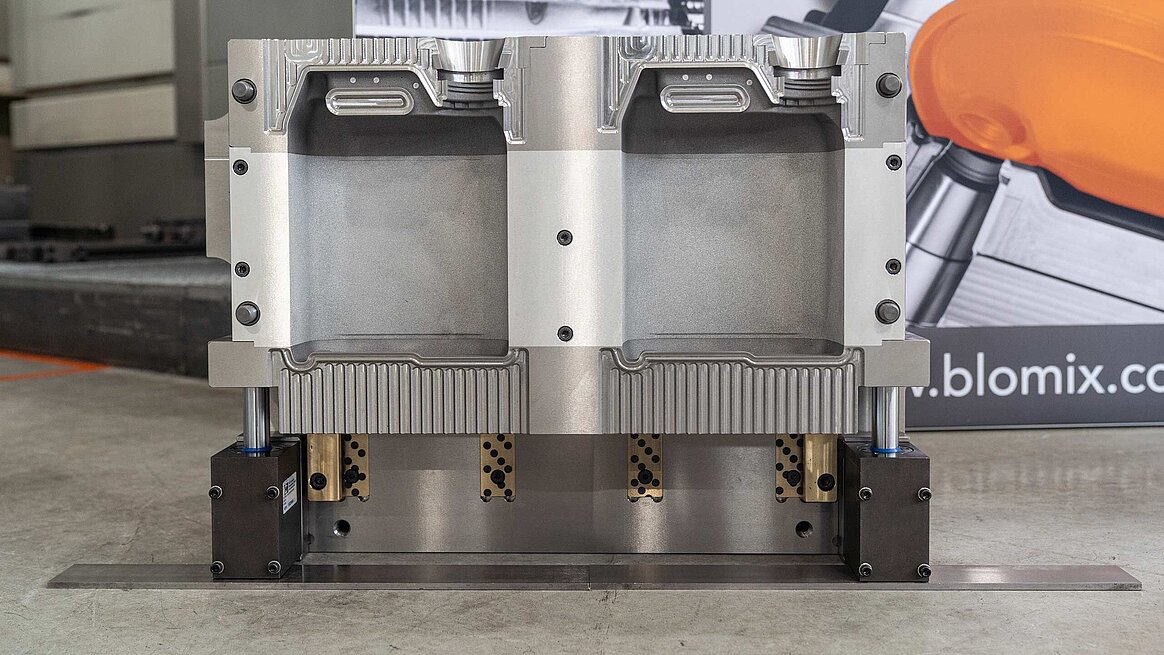
Uniform operation
Even though the HS flex heavy system is new, the team at BLOMIX found it easy to operate right from the start: Like the flexible handling system of the C 400 U, the heavy variant is controlled and managed by the Hermle Automation Control System (HACS). Hermle has developed the intelligent order management solution specifically to make access to the milling machine and automation as efficient, convenient and intuitive as possible. To stop his engineers from working on the disused machine out of old habit, Beenders resorted to using a somewhat unusual but extremely effective object – a padlock. "I would've handed over the key in exchange for a plausible explanation. But to this day it's remained untouched in my drawer."
Beenders is delighted with the integrated operating concept of the machining centres: "In our case, flexibility doesn't just mean we can easily swap parts between the three Hermle machines, it also means operators are proficient on each machine." They can thus optimise machine utilisation, thereby ensuring greater capacity. Room for improvement is important at the company, which works in a project-based manner. "We don't utilise the machines to maximum effect as this allows us to respond more spontaneously to requests from customers. Nevertheless, it has to worth our while," the Managing Director explains. His goal is to make the best possible use of automation and thus increase profitability. During the day, workers complete the complex tasks, perform tests and prepare the unmanned shifts. At night and on weekends, the 5-axis machining centres ideally run autonomously. "It's a mechanical sport, so to speak.
We don't want to be the biggest, but we want to remain the best," Beenders explains. "We achieve this goal through our adherence to deadlines and high-quality standards. And we can only do this with partners like Hermle, which keeps its promises in terms of precision, reliability and service." Nevertheless, Beenders still hesitated briefly before purchasing the C 650 U. The reason for this was the tool length. "The maximum length possible at present is 350 millimetres. For some geometries, however, we occasionally need tools measuring up to 500 millimetres in length, which can only be inserted manually." Fortunately, this was the only thing he had to compromise on with regard to the C 650 U the Managing Director admits. "Overall, we're extremely satisfied." Beenders is now planning to introduce new ERP software and improve how the machines are interlinked. And he knows for sure that: If a new machine is required, only an automated one comes into the equation.