The new one's name is Alberta
Lengthening spindle runtimes and making use of night-time hours – P&S Maschinenbau is capitalising on automation with the new HERMLE C 32 U HS flex. The company will use it to produce workpieces for its own machines for cutting and grinding, but will also manufacture high-precision special components for customer orders.
Zenz made its way to Cham about 30 years ago and was followed after some time by Wally, Susi, Sofie, Nelly, Luise, Lola and many others. And now Alberta has found a new home at P&S Maschinenbau. The manufacturing hall where these "ladies" are ensconced exudes order and tranquillity – the floor and equipment are immaculately neat. Each of the machines processes its tasks precisely in one of the rooms.
P&S Maschinenbau produces high-precision parts as a contract manufacturer for medical technology, the film industry and special machine construction in Cham, located in the east Bavarian administrative district of Oberpfalz. In addition to simple lathe and milling work, the company also refines aluminium parts by means of anodising. This makes it possible to design components in colour, for example, or to protect them against wear. Another mainstay is internal development projects: P&S has made a name for itself in tool making with carbide separating machines, step loaders and chamfering grinding machines. And all of the contract manufacturer's machining centres have a name. The employees get together and decide what a new machine should be called. Along with traditional names, names of family members can be chosen – a sort of godmother.
Walter Peter and Max Stahl founded the company in 1996 in Roding, about 20 kilometres from Cham. At first the machine park was easily manageable, consisting of a CNC milling machine, a cylinder-controlled lathe, a boring machine and a band saw. High manufacturing depth was important for the company founders from the beginning. "Our first milling machine was Zenz", recalls Max Stahl. This was the beginning of the path to a successful company which now has 100 employees. Every one to two years the company invests in new machines. The eleventh machining centre from HERMLE was added in 2022, this time a C 32 U HS flex.
Creating free capacity
The C 32 U HS flex is named appropriately – thanks to the HS flex handling system, it guarantees a high degree of automation and a wide bandwidth of products. Thus P&S Maschinenbau is able to run unsupervised shifts during the night. "Up to now we manufactured workpieces for our own machines in small series on our other HERMLE machining centres", explains Managing Director Max Stahl. "Now we have combined all of them on the new C 32", adds Managing Director Walter Peter. This allows the contract manufacturer to create capacity for individual parts again on other milling machines.
P&S intends to utilise about 50 percent of the capacity of the new HERMLE machine for its own workpieces. The other half will be for customer parts. The specialist manufactures holders for lenses, for example. The shape of the blanks is processed by turning and milling. Threads, grooves and fixtures ensure that the lenses will later be securely seated. Finally the company treats the surface in its own anodising plant to further improve the mechanical properties. "With our milled parts we have reached the limits of what is technically feasible. These limits include extremely thin walls and extraordinary precision, explains Walter Peter. In addition to aluminium, P&S processes stainless steel and tool steel as well as glass fibre-reinforced plastic (GFRP) to a limited extent.
-
Lukas Albert checks the fit of the workpiece. -
The P&S team: Alexander Roider, Production Manager; Lukas Albert, qualified employee on the C 32 U and Max Stahl, Managing Director (l to r). -
Lukas Albert is one of two qualified employees who operate and program the C 32 U HS flex. -
Each machining centre at P&S Maschinenbau has a female name – this makes it easy to clearly recognise the corresponding components.
In tiptop condition
The production halls reflect precision and a love for detail. We walk past Sofie, Luise and Lola and come to Alberta. We cannot help but notice the profusion of light, the complete absence of chips on the floor and that all the systems look like new. "Our series 40 from HERMLE is 23 years old now and still accurate to within a hundredth. That's incredible", says Max Stahl. And he adds: "We care for our machines, carry out inspections regularly and program neatly." and there is one more critical factor for high precision in manufacturing: qualified employees. "We employ exclusively qualified employees on our machines, foremen and technicians", says Walter Peter. They are able to operate the machines and control unit independently and some of them are familiar with CAD.
Initial and advanced training are a matter of course for the company. "We would like to make our jobs interesting so we can retain employees. An appropriate salary is just one pillar. Ongoing professional development is another", confirms Max Stahl. Therefore P&S Maschinenbau also relies on the next generation of employees and trains young people every year. "Our trainees receive the P&S gene", he grins. "They are very good when they complete their training. Some of them deepen their knowledge and then come back to us as foremen, technicians or engineers. We're very proud of that", says Walter Peter.
But good personnel are rare. Therefore P&S Maschinenbau now relies on automation. "We want long spindle runtimes, but our employees should not have to work until midnight to achieve this", emphasises Max Stahl. "That was one of the reasons why we chose the new C 32 U HS flex." The HS flex handling system enables the user to prepare pallets on 20 storage locations. It takes care of loading and unloading the machining centre – unsupervised and for example during the night shift. "This was a new technology for us", recalls Max Stahl. "It allows us to manufacture small batch sizes flexibly and automatically. That is an excellent fit with our high-mix low-volume approach." In this way the company can run the machining centre longer without operators and set it up faster. The additional magazine ZM 216, which increases the 36 tools in the C 32 U with an additional 216 tools, also contributes to this.
Tradition meets innovation
"What I especially like about HERMLE machines is the clear product line", says Max Stahl, explaining the basis of his decision. "For example, HERMLE offers a consistent and above all a well-engineered solution for its five-axis machining centres – from the smallest to the largest system. And they have been doing this for a long time. The training period is minimal and the precision is top-notch". "We sell our parts straight off the milling machine. We have no additional final check, reports Max Stahl. If there is a fitting that is not right, that is obvious on the machining centre so that faulty parts never even make it to the customer. "Our employees are personally responsible and that works very well for us", says Production Manager Alexander Roider, visibly pleased.
There was a challenge with the new acquisition, however, due to the HS flex handling system. "We manufacture chaotically, but we have seamless time recording in the company. When the new C 32 U HS flex changes a pallet at three in the morning, there is no employee at the machine to record the time. But that was one of our requirements for the new machining centre", emphasises Max Stahl. Manfred Pantel, of HERMLE sales field office in Bavaria, explains: "The machine logs everything, we just had to make the data available to P&S." Max Stahl is pleased: "Now we have an overview of all the machine runtimes and we know what the machining times were for individual parts. That is incorporated into our calculations."
"We also had to develop a feel for which parts fit best on the machine when", adds Alexander Roider. That may mean for example that unsupervised, non-critical processes such as roughing run at night, while precise fittings are made during the day when qualified employees are on site.
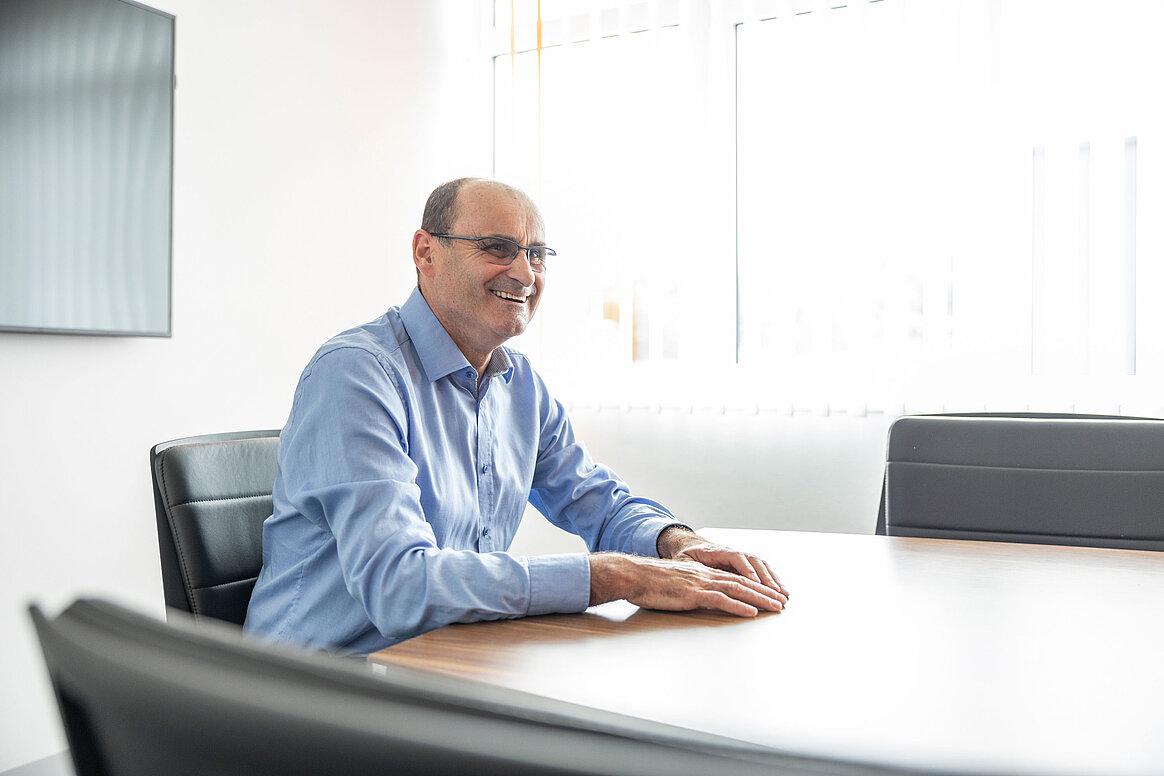
Competent support
The contract manufacturer is impressed by something else about HERMLE: its customer service. He points out that the contact person on the phone is always competent and able to answer all questions quickly and correctly. Replacement parts are usually there on the next day, he continues, and if the need arises, the HERMLE fitter is also there at the machine after no more than 48 hours. Production Manager Alexander Roider goes to the heart of the matter: "The service is super". "For me, half of sales is customer service. We have really seen this exemplified in HERMLE", says Max Stahl with a wink. "We also have outstanding people who do good work."
But why is the new HERMLE machine now called Alberta? "Lukas Albert is one of the two operators and programmers on the C 32 U HS flex", explains Alexander Roider. "He does great work, and in his honour we named the machine Alberta."