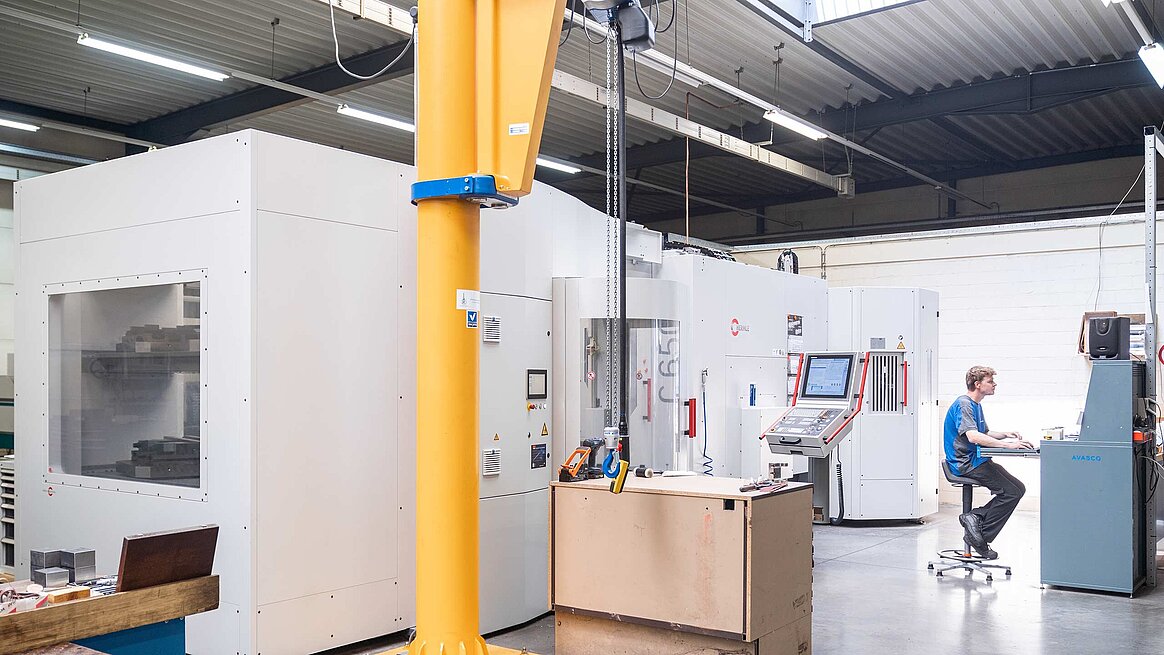
5-axis technology: Brake and accelerator
Even though the C 650 U has been up and running for about a year, the operators are not yet able to fully utilise the new capacities. “However, if there is a chance of using the C 650 U, the 5-axis machine is always the first choice,” stresses Deneire. So, where is the problem? “The most difficult part is in fact the extra axes compared to the C 400 V. We only recently entered the world of 5-axis machining and this still requires a bit of rethinking. However, we have also discovered that we can produce parts faster and run completely new machining processes than on our 3-axis machine,” adds the production manager. For instance, the new Hermle machine replaces a production step at the spark eroding machine – thus reducing the machining time from 40 to just 5 hours.
In contrast, the operators soon came to terms with the automation, even though it was a completely new concept for Cafmeyer. The same applies to the Heidenhein control unit, which they already knew in principle from the existing Hermle machine. “In total, we had eight days of training: Four immediately after installation and another four a few weeks later once the operators had become familiarised with the C 650 U and HS flex heavy,” explains Deneire. Since then, the employees have continued to make progress and learned to trust their programming skills and the machine. Should the tool and the workpiece nevertheless collide, Van Houtte has the peace of mind that Hermle uses compression sleeves to protect its spindles from greater damage, thus avoiding longer machine downtime.
Cafmeyer currently uses the C 650 U in particular for its mould making processes. In the future, it will also be used to produce milled parts for other companies. “The C 650 U opens up a whole host of opportunities. And Hermle has significantly raised the standards in terms of the support we now expect from our other service suppliers,” concludes Frederik Deneire, who had not worked with Hermle before joining Cafmeyer in February 2021.