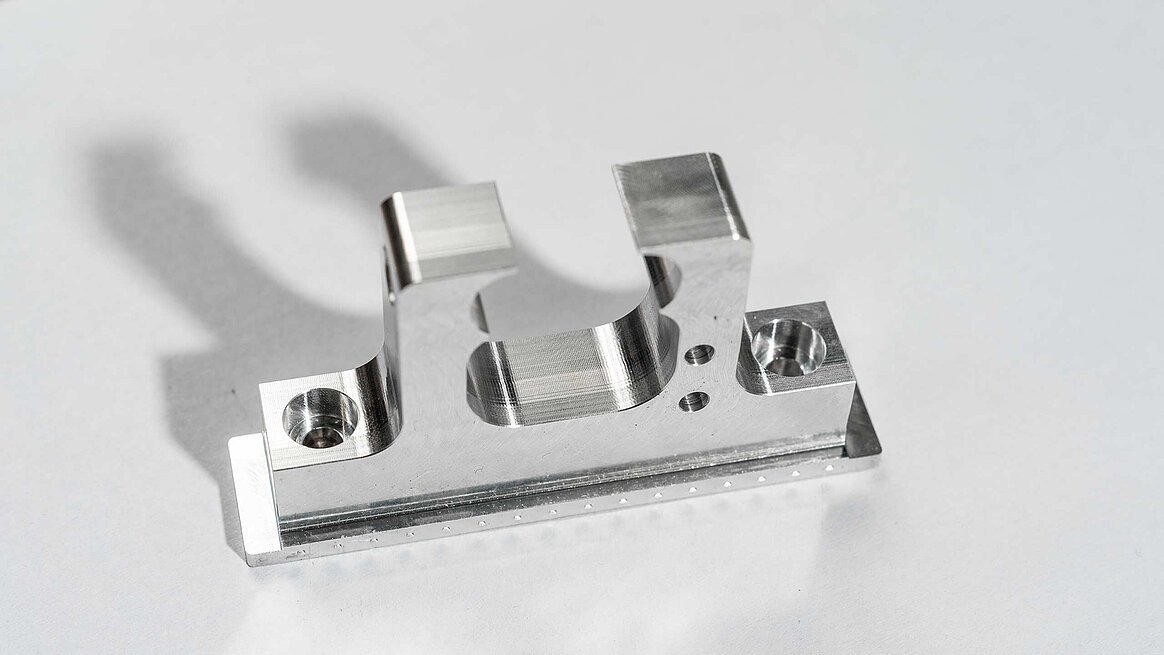
Stimmiges Gesamtkonzept
Die Aufspannfläche des 450 Kilogramm tragenden Schwenkrundtischs beträgt im Durchmesser 440 Millimeter. Dem hohen Anspruch an die Präzision wird auch der Schneckenantrieb gerecht, der zuverlässig Wellentorsion am Tisch verhindert. Der Verfahrweg liegt bei je 800 Millimetern in X- und Y-Richtung sowie bei maximal 550 Millimetern in Z-Richtung. „Das deckt einen Großteil unserer Werkstückdimensionen ab“, weiß Fertigungsleiter Christian Wensing, der sich als Projektverantwortlicher schon im Vorfeld nicht nur mit den zu bearbeitenden Werkstückmaßen, sondern auch mit den Anforderungen an die Automationslösung eingehend beschäftigt hat: „Da wir neu in die Automatisierung einsteigen, wollten wir ein System aus einer Hand mit möglichst wenig Fremd-Schnittstellen, die sonst zu Komplikationen führen können.“
Generell spielt die Prozesssicherheit eine große Rolle für das Maschinenbauunternehmen, das Fehler durch Standardisierung, Simulation und Kontrollmessungen zu vermeiden versucht. „Wir setzen nur standardisierte Spannmittel ein, die auch in unserem 3D-System abgebildet werden“, bestätigt Wensing. Ebenso standardisiert sind die Werkzeuge, deren Länge von der Anlage automatisch überprüft werden. Auch die Werkstücklage wird vor der Bearbeitung von der C 42 U automatisch kontrolliert. „Falls etwas nicht stimmt, wird die Palette gesperrt und gegen einen anderen Auftrag getauscht“, erklärt der Fertigungsleiter. „Zusätzliche Messzyklen kosten zwar Zeit, dienen aber der Sicherheit und Präzision. Diese sind uns extrem wichtig“, verdeutlicht der Geschäftsführer.
Der hohe Anspruch an Präzision und Sicherheit erklärt auch, warum die C 42 U vorerst nur 16 Stunden am Tag arbeitet. Zunächst will der Fertigungsleiter ein möglichst breites Teilespektrum unter direkter Aufsicht produzieren lassen. Das Ziel, die sichere vollautomatisierte Einzelteilfertigung auch über Nacht, sieht er jedoch innerhalb der nächsten Monate realisierbar. Steigt die Zahl der sich wiederholenden Teile, plant er den Betrieb in der mannlosen Schicht ein.
Auch wenn das Thema Automatisierung in der Firma Horstmann relativ jung ist, weiß der Fertigungsleiter die Möglichkeiten, die Hermle der C 42 U mitgibt, weitreichend zu nutzen. Das optionale Steuerungstool HIMS (Hermle Information Monitoring System) zeigt den Live-Status der Maschine an und versendet Ereignisse per E-Mail. Er erklärt weiterhin: „Wir bekommen die Produktionszeiten vollautomatisiert direkt von der Maschine in das ERP-System gemeldet. Dadurch können wir die Maschine ideal bebuchen.“ So ist das Bearbeitungszentrum schon wenige Monate nach der Inbetriebnahme an einem 16-Stunden-Tag zu bis zu 90 Prozent ausgelastet.
Dieser Erfolg ist auch der Unterstützung durch Hermle zuzuschreiben. „Der Service ist ein überzeugendes Alleinstellungsmerkmal“, lobt Klaus Horstmann die Zusammenarbeit mit den Baden-Württembergern. „Und wir haben durch dieses Projekt viele unserer Visionen realisieren können.“ So konnte er die Produktivität steigern und die Personalquote halten. Er entlastet seine Mitarbeiter von banalen oder körperlich anstrengenden Tätigkeiten, so dass diese ihr Potenzial und Know-how besser einbringen können.
„Das Bearbeitungszentrum von Hermle hilft uns zudem, unserem Kundenversprechen treu zu bleiben: hohe Servicequalität, kurze Reaktionszeiten und eine ständige Bereitschaft“, ergänzt der Geschäftsführer. Mit dem Projekt beweist er, dass auch kleine Unternehmen ihre Prozesse neu denken und flexibel sein können. „Wir können jetzt ganz weit vorne mitschwimmen“, sagt Horstmann abschließend.